Mastering the Art of Making Carbon Fiber Body Panels
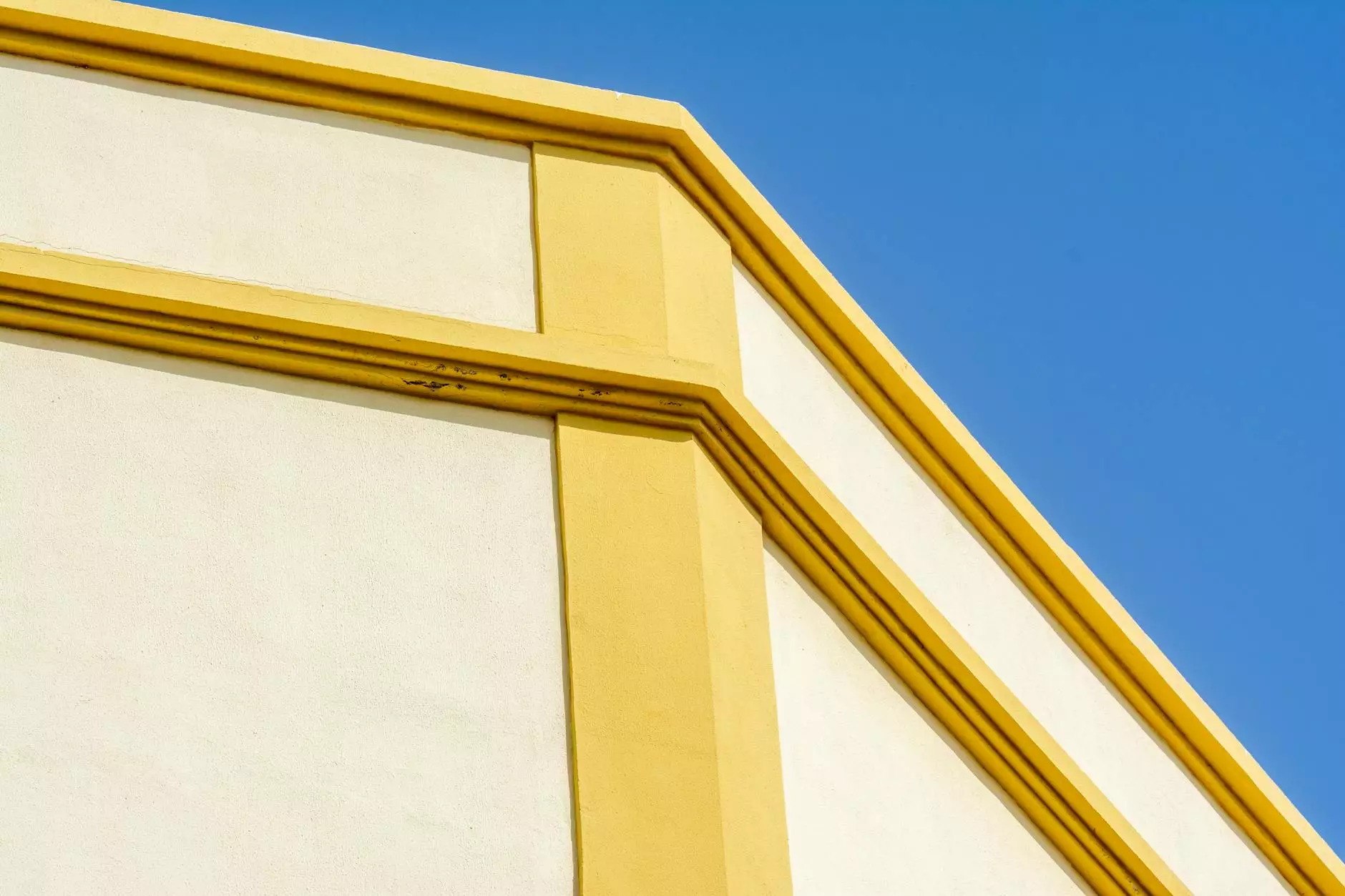
In today's fast-paced automotive industry, making carbon fiber body panels has emerged as a revolutionary technique that is capturing the attention of car manufacturers, enthusiasts, and aftermarket suppliers alike. The evolution of materials technology has paved the way for carbon fiber to play a central role in the production of vehicle components. This article aims to explore the comprehensive process of making carbon fiber body panels, their benefits, and their growing significance in the automotive sector.
Understanding Carbon Fiber
Before diving into the details of the making carbon fiber body panels, it is essential to understand what carbon fiber is. Carbon fiber is a high-strength, lightweight material composed of thin strands of carbon atoms. These fibers are typically combined with a resin, creating a composite material that possesses remarkable strength-to-weight ratios.
Properties of Carbon Fiber
- Lightweight: Carbon fiber panels are significantly lighter than their metal counterparts, leading to better fuel efficiency and performance.
- High Strength: Carbon fiber exhibits exceptional tensile strength, making it ideal for structural components in vehicles.
- Corrosion Resistance: Unlike metals, carbon fiber does not rust, making it suitable for various environmental conditions.
- Customizability: Carbon fiber can be molded into complex shapes, allowing for innovative designs and styles.
The Process of Making Carbon Fiber Body Panels
The process of making carbon fiber body panels involves several stages, each critical to ensuring the final product meets the required standards for automotive applications. Here’s a detailed breakdown of the steps involved in production:
1. Material Selection
The first step in the making carbon fiber body panels process is selecting the appropriate materials. This includes choosing the right type of carbon fiber, typically characterized by its fiber thickness and weave pattern.
2. Design and Engineering
Once the materials are ready, engineers and designers collaborate to create detailed specifications and design prototypes. These include CAD (Computer-Aided Design) models that allow for precision in design and ensuring the panels fit perfectly on the vehicle.
3. Layup Process
The layup process involves layering sheets of carbon fiber fabric into molds. Resins are used as an adhesive between the layers. This process can be done by hand or through automated methods, depending on the scale of production.
4. Curing
After the layup, the panels undergo curing—a heating process that solidifies the resin and strengthens the carbon fiber structure. This can be done in an autoclave, where pressure and temperature are carefully controlled to achieve optimal curing.
5. Finishing
Once cured, the carbon fiber panels are removed from the mold and undergo finishing processes, which may include sanding, painting, and applying protective coatings to enhance appearance and durability.
Benefits of Carbon Fiber Body Panels
The adoption of carbon fiber body panels offers a plethora of advantages for the automotive industry:
- Enhanced Performance: By reducing weight, carbon fiber panels improve vehicle speed and fuel efficiency, making them popular in racing and high-performance vehicles.
- Safety Improvements: Carbon fiber’s strength can help enhance vehicle safety by better managing impact forces during collisions.
- Design Flexibility: The ability to mold carbon fiber allows for custom body panels, enabling unique designs that can set a brand apart from competitors.
- Increased Resale Value: Vehicles with carbon fiber components can retain higher resale values due to their advanced features and performance attributes.
Applications of Carbon Fiber Body Panels
Carbon fiber body panels are not limited to high-end sports cars; their applications range across various segments of the automotive industry:
- Automotive Racing: Performance vehicles benefit immensely from the use of carbon fiber due to its lightweight and strength features.
- Luxury Cars: Premium automotive brands utilize carbon fiber to enhance aesthetics and performance, appealing to affluent customers.
- Electric Vehicles: Manufacturers of electric cars are increasingly using carbon fiber to offset weight, thereby extending range efficiency.
- Aftermarket Modifications: Car enthusiasts often look for carbon fiber body panels to upgrade their vehicles and achieve custom looks.
Future of Carbon Fiber in Automotive Industry
The future of making carbon fiber body panels looks promising. With advancements in manufacturing processes such as automated fiber placement (AFP) and 3D printing, the production of carbon fiber components is becoming more efficient and cost-effective. Additionally, as sustainability continues to gain traction in the automotive industry, researchers are exploring bio-based resins and recycled carbon fibers, which could further enhance the appeal of using carbon fiber materials.
Challenges in Production
Despite the advantages, there are challenges associated with carbon fiber production:
- High Manufacturing Costs: The initial costs of carbon fiber production can be higher than traditional materials, although prices have been decreasing gradually with advancements in technology.
- Complex Repair Processes: If damaged, repair processes for carbon fiber can be more complicated compared to metal, requiring specialized techniques and equipment.
Conclusion
Making carbon fiber body panels is transforming the automotive industry by offering lightweight, durable, and aesthetically pleasing options for vehicle manufacturers, dealers, and consumers alike. By utilizing carbon fiber, the automotive industry can achieve higher performance, improved safety, and cutting-edge designs that entice modern drivers.
As technology progresses and the demand for efficient and sustainable solutions increases, carbon fiber is poised to remain a critical material in automotive innovation. For businesses like customclass.net, offering solutions in auto parts and supplies will help capitalize on this trend, ensuring that enthusiasts and manufacturers can enjoy the myriad of benefits that carbon fiber has to offer.