The Ultimate Guide to Design for Additive Manufacturing
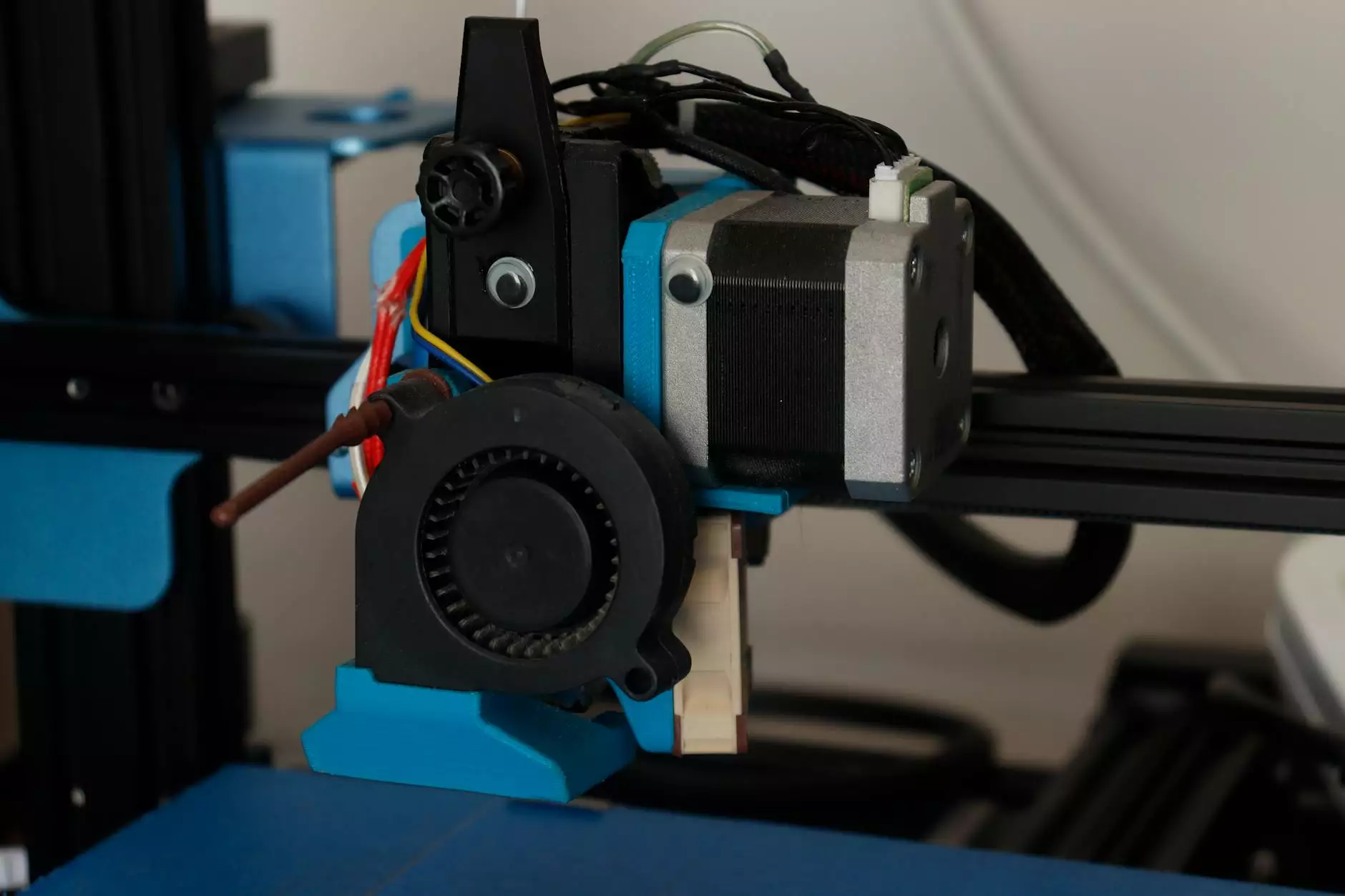
Design for Additive Manufacturing (DfAM) represents a paradigm shift in how businesses approach product creation and innovation. This article delves deep into the intricacies of DfAM, showcasing its significance, applications, and the transformative impact it has on industries such as art supplies, product design, and 3D printing. Our mission is to equip you with the knowledge needed to utilize DfAM effectively, ensuring your business stands out in a competitive marketplace.
Understanding Design for Additive Manufacturing
At its core, design for additive manufacturing refers to the strategic approach of designing products specifically for 3D printing technologies. Unlike traditional manufacturing methods, which limit design freedom due to tooling and material constraints, DfAM allows for a level of creativity and innovation previously unimaginable.
Key Principles of DfAM
- Complexity is Free: In additive processes, complex geometries can be produced easily, often with little additional cost.
- Minimize Material Usage: DfAM promotes the use of material-saving techniques that can lead to lighter and more efficient designs.
- Designing for Assembly: Streamlining parts to reduce assembly time and improve functionality is a critical aspect.
- Customization and Personalization: DfAM enables tailored products that meet individual customer needs without significant cost increases.
The Impact of DfAM on Various Industries
The introduction of design for additive manufacturing has been groundbreaking across several sectors, each reaping unique benefits:
1. Art Supplies
In the realm of art supplies, DfAM is revolutionizing how artists and designers create tools and components. Instead of relying on mass-produced items that may not suit individual artistic visions, 3D printing technologies allow for customized tools such as:
- Unique sculpting tools
- Personalized paint dispensing devices
- Tailored design stencils and templates
Artists can now push their creative boundaries, crafting pieces that are not only original but also expressive of their unique styles.
2. Product Design
In product design, DfAM opens a world of possibilities. Designers can create intricate structures that enhance both aesthetic appeal and functionality. For instance:
- Prototyping becomes faster and more cost-effective, allowing for rapid iterations based on user feedback.
- Innovative structures that combine different materials can be produced, improving product performance.
- Direct-to-consumer models become feasible, where a product can be designed and delivered in a fraction of the time traditionally required.
This shift not only enhances creativity but also provides a competitive edge in the market.
3. 3D Printing
The field of 3D printing thrives on DfAM practices. Advanced software and tools specifically built for DfAM allow companies to explore:
- Topology optimization to minimize material waste
- Designing for Multi-Material Printing which combines different materials for advanced product features
- Adaptive design strategies that change based on printer capabilities and material behavior
These advancements are not just theoretical; they are being applied in industries ranging from aerospace to healthcare, where precision and innovation are paramount.
Challenges in Implementing DfAM
Despite its vast potential, implementing design for additive manufacturing is not without challenges. Understanding these hurdles can prepare your business for successful integration:
1. Skill Gaps
One of the most pressing challenges is the skill set required for effective DfAM. Traditional designers might not have the technical knowledge of 3D printing processes or materials.
2. Software Compatibility
Ensuring software compatibility is vital. Many designers employ various CAD tools that may not fully integrate with 3D printing technologies, leading to inefficiencies.
3. Material Limitations
While DfAM allows for greater design freedom, the selection of materials compatible with 3D printing is still somewhat limited compared to traditional manufacturing methods.
Strategies for Successful DfAM Adoption
To overcome these challenges and embrace design for additive manufacturing effectively, consider the following strategies:
1. Invest in Training
Providing training opportunities for designers on DfAM principles can significantly enhance their capability to create innovative designs. Workshops and online courses are widely available and can bridge the knowledge gap.
2. Collaborate with Experts
Partnering with experts in 3D printing technology can offer insights that drive innovation. They can help navigate software and material challenges, ensuring a smoother transition.
3. Prototype and Test
Implementing a culture of rapid prototyping allows businesses to test designs thoroughly before full-scale production. This iterative process helps refine products and enhance their effectiveness.
The Future of Design for Additive Manufacturing
The future of design for additive manufacturing appears promising. As technology advances, we can anticipate:
1. Enhanced Materials
New materials are being developed that can withstand even greater stresses and strains, opening up applications in fields like aerospace and automotive engineering.
2. Integrated Workflows
As software solutions improve, the design-to-manufacturing workflow will become more streamlined, making it easier for designers to create optimized products without being bogged down by technical limitations.
3. Sustainability Focus
With growing emphasis on environmentally friendly practices, DfAM will likely focus on sustainable materials and processes, aiming to reduce waste and enhance recyclability.
Conclusion: Embracing DfAM for Business Success
Design for additive manufacturing is not just a trend; it is a critical component that businesses must embrace to remain competitive in today's fast-paced market. By understanding its principles, applications, and potential challenges, companies can leverage DfAM to create innovative products that resonate with modern consumers.
As you navigate through the realm of art supplies, product design, and 3D printing, embracing DfAM will undoubtedly position your business for success. Be proactive, invest in the necessary training, and stay agile in adapting to new technologies, ensuring your establishment remains at the forefront of this innovative field. The time to act is now!